Sicherheitstechnischer Hintergrund
Auslöser für die Empfehlung der Western European Nuclear Regulators Association (WENRA) waren die Befunde bei wiederkehrenden Prüfungen an den Reaktordruckbehältern der belgischen Druckwasserreaktoren des Lieferanten Westinghouse, die als Wasserstoffflocken, die während des Herstellungsprozesses ins Grundmaterial gelangten, interpretiert wurden.
Aufgrund der in Belgien festgestellten Anzeigen (Abbildung 1) hat die WENRA im Sommer 2013 die Empfehlung „Recommendation in connection with flaw indications found in Belgian reactors“ an ihre Mitglieder herausgegeben. Darin wird den Aufsichtsbehörden eine zweistufige Verifikation von Werkstoffqualität und struktureller Integrität der Reaktordruckbehälter (RDB) empfohlen:
– 1. Schritt: Überprüfung der Herstellungsdokumentation
„...review and compile a
chronological and comprehensive documentation of all processes and steps of the manufacturing and controls of the RPV forgings and to evaluate this documentation with respect to the hydrogen flaking issue.... „
– 2. Schritt: Prüfungen am RDB-Grundmaterial
„... The inspections should cover a
representative volume of RPV forging base material in areas known to be potentially susceptible to hydrogen flaking. If these inspections reveal evidence of hydrogen flaking the inspections should be extended appropriately.... „
Das ENSI hat diese Empfehlungen aufgenommen und mit zwei Forderungen gegenüber dem Kernkraftwerk Gösgen (KKG) umgesetzt:
– Brief vom 23.01.2013 [1]
Forderung 1:
Aufgrund der neuen Aspekte zu den Befunden von Doel-3 und Tihange-2 wird das KKG aufgefordert, dem ENSI bis zum 30.04.2013 eine Stellungnahme (technischer Bericht) einzureichen, der die Qualität des Grundmaterials des RDB beschreibt und nachweist. ...“
– Brief vom 04.07.2013 [2]
Forderung 2:
Das KKG hat ergänzende Ultraschallprüfungen am
Grundmaterial des RDB zum nächsten regulären Wiederholungsprüftermin des RDB durchzuführen…. Die Prüftechnik soll so
gewählt werden, dass mögliche wasserstoffinduzierte Fehler sicher gefunden werden können.„

Der Reaktordruckbehälter ist die wichtigste Barriere für den Einschluss der im Reaktorkern vorhandenen Reaktivität. Seine Integrität ist zugleich Voraussetzung für die Kühlung des Reaktors sowohl im Betrieb der Anlage als auch bei Störungen und Störfällen.
Das Vorhandensein von Wasserstoffflocken oder gegebenenfalls von Rissanzeigen im Grundmaterial ist von grundsätzlicher Bedeutung, da diese die Widerstandsfähigkeit des Reaktordruckbehälters nachteilig beeinflussen oder sogar schwächen können. Bezüglich von Belastungen im Normalbetrieb bestehen auslegungsgemäss grosse Sicherheitsreserven, da die Wandstärke des Druckbehälters entsprechend gewählt ist. Eine Beeinträchtigung für Normalbetriebslasten und betriebliche Störungen ist daher nur bei einer grossflächigen Schwächung des RDB möglich. Diese Beurteilung hat sich beim Beinaheunfall im amerikanischen Kernkraftwerk Davis-Besse in unbeabsichtigter Art und Weise bestätigt. Dort kam es infolge borinduzierter interkristalliner Spannungsrisskorrosion zu einem nahezu vollständigen lokalen Materialabtrag des Grundwerkstoffs bis auf die Plattierung, ohne dass es zu einem RDB-Leck kam.
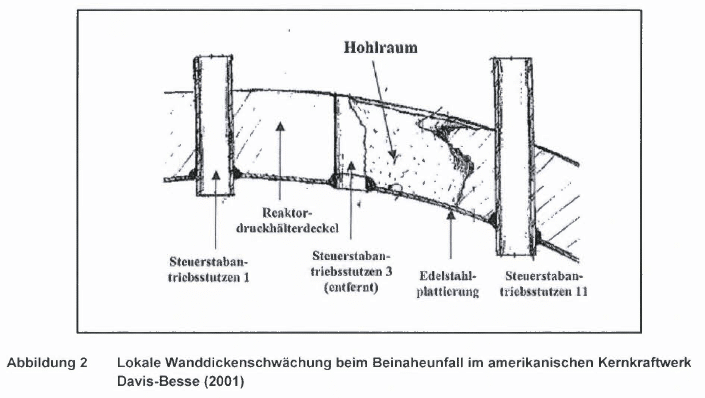
Für einen Druckbehälter westlicher Bauart, der nach üblichen Herstellungs- und Überwachungsverfahren gefertigt wurde, wird die Eintrittshäufigkeit für eine grössere Leckage am RDB international als kleiner als 10-7/a bewertet.
Als für die Lebensdauer eines RDB eines Druckwasserreaktors massgebender Lastfall wurden in Sicherheitsanalysen Kaltwassereinspeisungen unter hohem Druck bei Störfällen identifiziert. Das dabei auftretende Phänomen wird international als PTS (Pressurized Thermal Shock) bezeichnet. Es kann je nach Materialeigenschaften des RDB-Stahls unter den bei einem Störfall auftretenden Bedingungen potenziell zu einem RDB-Versagen führen. Phänomenologisch kann es bei einer sehr starken Reduktion der Temperatur des RDBs zu einer Veränderung des makroskopisch beobachtbaren Bruchverhaltens kommen. Diese Veränderung besteht in einem Übergang von einem dominant zähen Bruchverhalten zu einem dominant spröden Bruchverhalten (weitgehend verformungsloser Bruch, Bruchdehnung < 10%). Die Temperatur, bei der dieser Übergang erfolgt, wird als Sprödbruch-Übergangstemperatur bezeichnet. Diese Temperatur erhöht sich über die Lebensdauer eines Reaktordruckbehälters als Folge der Neutronenbestrahlung.
Um eine ausreichende Sicherheitsmarge gegen den Übergang zu einem spröden Versagensverhalten an Reaktordruckbehältern zu gewährleisten, werden im kerntechnischen Regelwerk Mindestanforderungen an die Sprödbruch-Übergangstemperatur (Vorgabe: eine Referenztemperatur RT
NDT, die sich infolge strahlungsinduzierter Versprödung einstellen darf) und an die Duktilität (zähes Werkstoffverhalten) formuliert, welche innerhalb der Lebensdauer eines Reaktordruckbehälters nicht verletzt werden dürfen. Zugleich wird festgelegt, wie die Sprödbruchübergangstemperatur (resp. die zugehörige Kerbschlagarbeit) experimentell zu bestimmen ist. Für westliche Reaktoren stutzt man sich dabei auf den NRC RG 1.99 (v.2) ab. In der Schweiz sind die Mindestanforderungen in der Verordnung des UVEK über die Methodik und die Randbedingungen zur Überprüfung der Kriterien für die vorläufige Ausserbetriebnahme von Kernkraftwerken (SR 732.114.5)“ [3], Artikel 4 vorgegeben. Bei Einhaltung dieser Bedingungen darf unterstellt werden, dass auch postulierte Risse mit Abmessungen im Bereich resp. oberhalb der Auflösungsgenauigkeit von zerstörungsfreien Werkstoffprüfungen auch unter Störfallbedingungen nicht unkontrolliert bis zu einem Versagen des RDB wachsen können. Das heisst, dass die Integrität des RDB auch unter abdeckenden Störfallbedingungen gegeben bleibt.
Nachweise werden auf der Grundlage der Werkstoffdaten mit Hilfe von Methoden der technischen Bruchmechanik durchgeführt, wobei die thermohydraulischen Randbedingungen, welche die Belastung des RDB charakterisieren aus Störfallanalysen abgeleitet werden. Der Versprödungszustand des RDB wird mit Hilfe von standardisierten Voreilproben bestimmt und überwacht.
Rissanzeigen oder Einschlüsse von Wasserstoff können die sicherheitstechnische Bewertung nachteilig beeinflussen. Beispielhaft können genannt werden:
- Vorhandensein von Rissen, die durch betriebliche Belastungen so wachsen können, dass bis zum Ende der geplanten Lebensdauer Rissgrössen erreicht werden, so dass ein Sicherheitsnachweis für abdeckende Störfallbedingungen für den erwarteten Versprödungszustand des RDB nicht mehr geführt werden kann,
- Schwächung der Materialkennwerte infolge grossflächigen Wasserstoffeintrags, der seinerseits auch die Bildung von neutronenflussinduzierten Fehlstellen fordern, und damit die Versprödung nachteilig beeinflussen kann.
Technisch können verschiedene Gegenmassnahmen zur Gewährleistung der Sicherheit getroffen werden, z.B.:
- Begrenzung der neutronenflussinduzierten Versprödung durch geeignete Beladung des Reaktorkerns („Low Leakage“ Beladung), was zu einer Reduktion des Neutronenflusses auf der RDB-Innenseite fuhrt,
- Reduktion der Störfallauswirkungen, z.B. durch Vorwärmen des bei Störfällen eingespeisten Notkühlmittels (Reduktion der Belastung bei Störfällen) oder Reduktion des Einspeisedruckes von Notkühlpumpen,
- Nachträgliche thermische Behandlung des RDB zur Verbesserung der mechanischen Eigenschaften („Glühen“),
- Beschränkung der Lebensdauer durch Festlegung einer höheren zulässigen Sprödbruchübergangstemperatur (entspricht einer geringeren zugelassenen Versprödung infolge Neutronenbestrahlung über die Lebensdauer des RDB).
Wie nachfolgend an Hand der Überprüfung des Herstellungsverfahrens und der positiven Ergebnisse der zerstörungsfreien Prüfungen aufgezeigt, besteht für das KKG keine Notwendigkeit für die Einleitung spezieller Massnahmen.
Beantwortung der Fragen
Erster Schritt: Analyse der Unterlagen
Welche Unterlagen standen zur Verfügung, welche Informationen zum Herstellungsprozess waren relevant?
Im KKG ist die vollständige Dokumentation zur Herstellung des Reaktordruckbehälters vorhanden. Für die Beurteilung hinsichtlich des möglichen Vorhandenseins von Wasserstoffflocken waren folgende Informationen relevant:
- Stahlherstellung -> Elektrostahl mit Vakuumentgasung entsprechend der Spezifikation
- Wärmebehandlungen der Schmiedeteile -> alle Wärmebehandlungen wurden spezifikationsgerecht durchgeführt
- Zwischenprüfungen -> keine registrierpflichtigen Anzeigen
- Fertigungsendprüfungen -> keine registrierpflichtigen Anzeigen
- Nullaufnahme des RDB (mechanisierte Ultraschallprüfung im eingebauten Zustand vor der Inbetriebnahme des KKG als Referenz für spätere Wiederholungsprüfungen) -> keine registrierpflichtigen Anzeigen
Wer hat den RDB hergestellt? Etappen des Prozesses?
Ein RDB-Unterteil wird typischerweise durch das Verschweissen von mehreren geschmiedeten Ringen hergestellt.
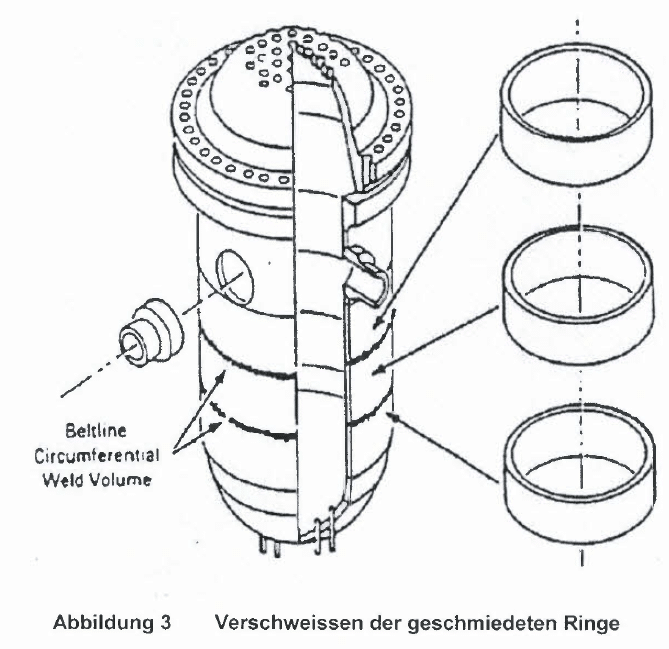
Der RDB des KKG besteht aus 2 Mantelringen und dem Stutzenring. An der Herstellung waren verschiedene Hersteller beteiligt:
- The Japan Steel Works Ltd.
Herstellung von 1 Mantelring (Giessen des Schmiedeblocks, Schmieden des Rings, mechanische Bearbeitung, 3-fache Zwischenprüfungen durch den Hersteller, Kraftwerk Union AG KWU [heute Areva NP] und unabhängig davon durch den Technischen Überwachungsverein (TÜV)
Herstellung von 1 Mantelring und vom Stutzenring (Giessen der Schmiedeblöcke, Schmieden der Ringe, mechanische Bearbeitung, 3-fache Zwischenprüfungen durch den Hersteller, KWU und unabhängig davon durch den TÜV)
Endfertigung des RDB durch Verschweissen der Ringe, Aufbringen der Plattierung, mechanische Bearbeitung, diverse Wärmebehandlungen, 3-fache Zwischen- und Endprüfungen durch den Hersteller, KWU und den Schweizerischen Verein für Druckbehälterüberwachung (heute Schweizerischer Verein Technischer Inspektionen SVTI).
Hat damals die Akzeptanzprüfung zu Anzeigen geführt, die innerhalb der Akzeptanzgrenzen waren?
Bei allen Zwischen- und Endprüfungen der Mantelringe und des Stutzenrings wurden weder registrier- noch bewertungspflichtige Anzeigen festgestellt.
Welche Anzeigengrösse wurde damals toleriert, wo lagen die Akzeptanzgrenzen?
Als Registriergrenze für die Fertigungsendprüfungen am RDB-Mantel war eine Ersatzfehlergrösse von Kreisscheibenreflektor (KSR) = 3 mm festgelegt. D.h. ein Ultraschallreflektor, der dem Reflexionsverhalten eines KSR von 3 mm Durchmesser entspricht, musste im Prüfprotokoll festgehalten werden. Als Akzeptanzgrenzen waren, in Abhängigkeit von der Wanddicke, grössere Ersatzfehlergrössen festgelegt.
Zweiter Schritt: Ultraschall-Messungen Revision 2015
Umfang der Messungen?
Der Prüfumfang betrug 30%, aufgeteilt in 3 gleichmässig über den Umfang des RDB verteilte Segmente.
Welches Messgerät wurde eingesetzt? Wie läuft die Prüfung technisch ab?
Die Prüfung wurde wie gefordert mittels eines Ultraschallprüfverfahrens durchgeführt. Bei einer RDB-Prüfung mittels Ultraschall können grundsätzlich zwei Verfahren unterschieden werden:
- Kontakttechnik
- der Prüfkopf liegt an der RDB-Innenwand an, das Wasser dient als Koppelmittel
- Tauchtechnik
- der Prüfkopf befindet sich in einem gewissen Abstand zur RDB-Innenwand, das Wasser bildet eine Vorlaufstrecke,
- Tauchtechnik
- in Frankreich eingesetzte Prüftechnik für Wiederholungsprüfungen,
- in Belgien eingesetzte Prüftechnik, mit der die Befunde festgestellt wurden,
- im KKG eingesetzte Prüftechnik zur Suche nach Wasserstoffflocken.
Vorgängig zur Prüfungsdurchführung wurde das gesamte Prüfsystem (d.h. Ultraschallprüfgerät, Manipulator, Prüfspezifikation und Prüfpersonal) erfolgreich einer Qualifizierung entsprechend den Vorgaben aus ENSI-B07 unterzogen. Damit wurde der Nachweis erbracht, dass das Prüfsystem geeignet ist, um Wasserstoffflocken aufzufinden. Zudem wurde es bereits vorgängig in anderen Kernkraftwerken für die von der WENRA empfohlenen Sonderprüfungen eingesetzt. Das verwendete handelsübliche Ultraschallprüfgerät hat die Bezeichnung „MicroPulse 5PA“.
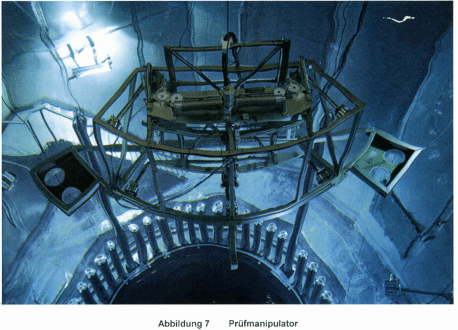
Die Prüfung ist wie folgt abgelaufen:
- Aufbau von Manipulator und Ultraschallprüfgerät im Reaktorgebäude
- Überprüfung aller Geräte auf korrekte Funktion
- Einjustieren des Ultraschallgeräts unter Aufsicht des Nuklearinspektorats des Schweizerischen Vereins Technischer Inspektionen (SVTI-N)
- Absenken des Manipulators (trägt den Ultraschallprüfkopf) in den mit Wasser gefüllten RDB
- Fahren des Manipulators entlang der vorgegebenen Spuren mit gleichzeitiger Aufnahme der Ultraschalldaten. Die Daten werden separat abgespeichert. Der SVTI-N überwacht, dass die Prüfung entsprechend der Prüfvorschrift durchgeführt wird.
- Wieder Hochholen des Manipulators, wenn alle Daten korrekt aufgenommen sind
- Ausjustieren des Ultraschallgeräts unter Aufsicht des SVTI-N
- Abbau von Manipulator und Ultraschallprüfgerät im Reaktorgebäude
- Analyse und Bewertung der aufgenommenen Daten unter Aufsicht des SVTI-N
Zusätzlich wurden Prüfungsdurchführung, Analyse und Bewertung der Daten durch einen Fachexperten des ENSI inspiziert.
Ergebnisse? Analyse? Bewertung?
Die Prüfdaten zeigten keinerlei Hinweise auf das Vorhandensein von Wasserstoffflocken. Das Ergebnis wurde vom Sachverständigen des SVTI-N bestätigt.
In der Pressemitteilung vom 06.07.2015 erklärte das ENSI:
„...Die Innenseite des Reaktordruckbehälters wurde umfassenden Ultraschallprüfungen unterzogen, wie sie alle zehn Jahre durchzuführen ist, sowie einer spezifischen Prüfung, die das ENSI nach der Meldung von Befunden in den belgischen Anlagen Doel-3 und Tihange-2 gefordert hatte. Die Prüfungen bestätigten seinen guten Zustand. ...„[1]
Die Anzeigen im Kernkraftwerk Beznau 1 und in den belgischen Reaktoren wurden im Grundmaterial festgestellt. Gesucht wurde damals jedoch nach Rissen unter der Plattierung wie es standardmässig in Frankreich gemacht wird (nach meinem Wissen alle 10 Jahre)? Dabei wurde ein französisches Messgerät (MIS) eingesetzt. Wurde in der Schweiz auch nach Rissen unter der Plattierung (undercladding cracks) gesucht, wie es standardmässig in Frankreich gemacht wird (nach meinem Wissen alle 10 Jahre)?
Der RDB des KKG ist mit einer 2-lagigen Plattierung ausgeführt. Die anlässlich der Fertigungsendprüfungen durchgeführten Prüfungen der Plattierung ergaben keine Hinweise auf das Vorhandensein von Unterplattierungsrissen. Das KKG hat anlässlich der RDB-Prüfung 1998 die wichtigsten Stellen (Grundmaterial unterhalb der Eintrittsstutzen, potentielle Gefährdung durch PTS) mittels Ultraschall nochmals auf Unterplattierungsrisse geprüft. Es zeigten sich erneut keinerlei Hinweise auf das Vorhandensein von Unterplattierungsrissen. Da es sich bei Unterplattierungsrissen um Herstellungsfehler und nicht um betriebsinduzierte Fehler handelt, kann auf weitere Prüfungen verzichtet werden.
Sind solche Prüfungen radiologisch relevant für das Personal?
Die in der Revision 2015 durchgeführten RDB-Prüfungen ergaben insgesamt eine Kollektivdosis von < 10 Pers. mSv (gesamte Kollektivdosis des KKG für das Jahr 2015: 493 Pers. mSv). An der Durchführung, Betreuung und Überwachung der RDB-Prüfungen waren über 20 Personen beteiligt. Somit ergibt sich für die einzelnen involvierten Personen keine bedeutende Dosisbelastung.
Sicherheitstechnische Beurteilung
Die Ergebnisse der Überprüfung des Herstellungsprozesses wie auch die durchgeführten Sonderprüfungen des RDB, welche aufgrund der Empfehlungen der WENRA und auf Anordnung des ENSI durchgeführt wurden, haben den sicheren Zustand des RDB des KKG bestätigt.
Literaturverzeichnis
[1] ENSI, Herstellungsfehler im Grundmaterial der ROB von Doel-3 und Tihange-2 – Stellungnahme zum Nachweis der Qualität des RDB – Geschäftsnummer:
17/13/005, 21. Januar 2013.
[2] ENSI, Herstellungsfehler im Grundmaterial der Reaktordruckbehälter von Doel-3 und Tihange-2 – Folgemassnahmen in der Schweiz – ENSI-Geschäft
17/13/005, 4. Juli 2013.
[3] UVEK,
Verordnung des UVEK über die Methodik und die Randbedingungen zur Überprüfung der Kriterien für die vorläufige Ausserbetriebnahme von Kernkraftwerken, 2009.
Grundlegende Begriffe
Wasserstoffflocken
Bei Wasserstoffflocken handelt es sich um Herstellungsfehler beim Schmieden. Sie treten typischerweise in dickwandigen Schmiedestücken auf. Die Ursache liegt darin, dass sich während des Schmelzens und Giessens im flüssigen Stahl Wasserstoff löst. Während der Erstarrung reichert er sich an lokalen Inhomogenitäten an. Bei der Abkühlung nach dem anschliessenden Schmieden kann der Partialdruck des Wasserstoffs zusammen mit hohen Eigenspannungen zur Bildung von feinen Rissen fuhren, den sogenannten Wasserstoffflocken. Sie können mit grosser Wahrscheinlichkeit vermieden werden durch
– Vakuumbehandlung des flüssigen Stahls,
– sehr langsame Abkühlung mit langer Haltezeit nach dem Schmieden.
Wiederholungsprüfungen
Für den RDB regelt die Festlegung NE-14 „Wiederholungsprüfungen von nuklear abnahmepflichtigen mechanischen Komponenten der Sicherheitsklassen 1 bis 4“ des SVTI-N den Umfang und die Anforderungen an die Wiederholungsprüfungen. Das Prüfkonzept beruht, entsprechend dem internationalen Stand der Technik, auf Stichprobenprüfungen. Der festgelegte Prüfumfang kann u.a. gezielt erweitert werden, wenn Mängel, Fehler oder Schäden in der eigenen oder in ähnlichen Anlagen festgestellt werden, die auf ein grundsätzliches, systematisches Problem hinweisen. Dies gilt insbesondere für das Vorhandensein spezieller Fehler aus der Herstellung. Werden bei der zerstörungsfreien Werkstoffprüfung Anzeigen festgestellt, so werden sie in folgende Kategorien eingeteilt:
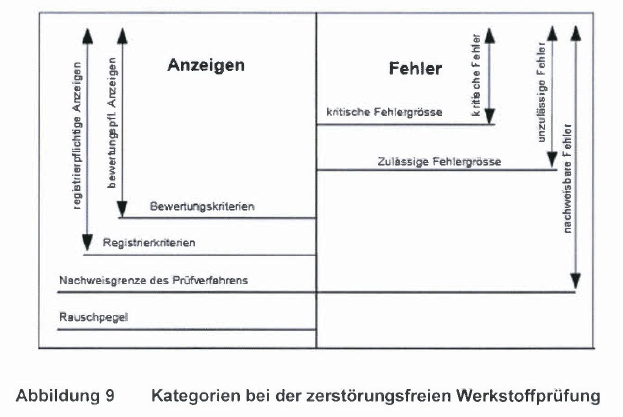
Gemäss der Richtlinie ENSI-B07 „Sicherheitstechnisch klassierte Behälter und Rohrleitungen: Qualifizierung der zerstörungsfreien Prüfungen“ muss für zerstörungsfreie Prüfungen vor dem Einsatz der systematische Nachweis erbracht werden, dass sie die erwartete Leistung unter Einsatzbedingungen erbringen.
[1] Ergänzung des ENSI: Es wurden keine registrierpflichtigen Anzeigen gemessen.
Präsentation der Vertreter des Kernkraftwerks Gösgen zur Prüfung des Reaktordrukcbehälter-Grundmaterials (Fage 25)